![]() |
---|
Shop Floor Integration MES for AX

Shop Floor Integration, also known as Manufacturing
Execution Systems (MES), provide manufacturers with
the ability to monitor and report on machines on the shop
floor, as well as manual processes through an automated
software system.
The Ellipse Solutions MES for Microsoft Dynamics® AX 2012 is a productivity tool that provides a
real-time automated approach to data collection and OEE metrics for visibility into what is
happening at each machine.
You gain:
-
Dashboard metrics your people can easily see.
-
Identify problems in real time for quicker resolution.
-
Watch productivity and profitability as it happens.
-
Plant wide productivity gains in the range of 10% to 50%.
-
Availability and Performance Metrics, Alarm Recording/Reason Codes.
-
Downtime/Reason Codes, Reject Counts/Reason Codes.
-
Schedule by Calendar Days, Run Hours or Power On Hours.
-
Advanced Reporting and Analysis.
The advanced functionality in Ellipse Solutions MES allows work order information to flow seamlessly from Microsoft Dynamics AX 2012 through the MES to the machine on the shop floor and back, delivering a paperless shop floor. This means all machines are integrated into a single system for one, holistic view of operations. In addition, your back office accounting and front office customer service are also integrated.
All of a sudden, things like billing release, inventory release, scrap write-offs and raw materials/finished goods entries can be automated as they happen. And since integration is bisynchronous, machine and job assignment scheduling can be adjusted and changed in real time for more efficient operational control.
-
Dynamics AX Production orders, items, machine operators, schedules, and other valuable data points are integrated and available on the shop floor.
-
Dynamics AX is automatically updated when a work order is started, production or setup hours are consumed and finished goods quantities are produced at the production lines
Worried your machines are too old or varied? Through our partnership with Memex Automation, we can provide an interface device that works with hundreds of protocols, and we add new ones every day. If your machine can be monitored, we can make it happen.
Efficiency Dashboard
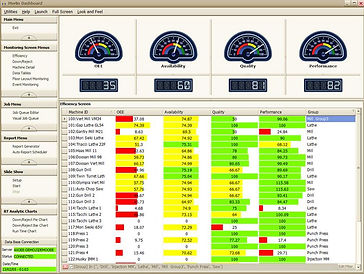
What is OEE? – Overall Equipment Effectiveness
OEE is a statistical measurement used to determine how efficiently a machine is running.
Features include:
-
Key performance indicator
-
Real-time production visibility for everyone in the plant including alerts through email or paging
-
Accurate key performance indicator with OEE metric
-
Identify problems fast
-
Production data collection and reporting
-
Downtime and reject cause analysis
-
Labor productivity tracking
-
Usage-based preventative maintenance
-
Visual production scheduling
-
Connection production floor to ERP
-
Assess operator productivity
-
Hardware, firmware and software all connected to the machine
-
Software for plant wide metrics
-
Handhelds, scanners, bar codes, marquees, light trees, devices ect.
-
Real-time connection to machines
-
Over 400 data elements collected
-
Comprehensive reporting in 8 ways
-
Reports, web, email alerts, real-time dashboard, cycle charts, KPI’s, down/reject, schedule)
Machine Detail Page

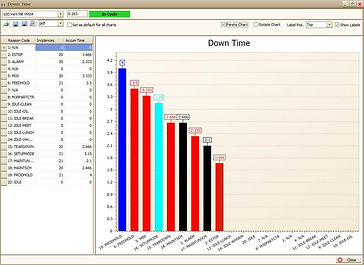
Smart Equipment = Smart Factories = Profitability
Make every factory machine into a node on your corporate network.
-
Every machine can be IP addressable and therefore a secure node on the corporate network.
-
Make the information about the machine and production, including history, available on your network.
-
Embed web connectivity to provide Intranet or Internet Access to real time factory data.
-
Integrate all factory equipment into into all ERP Capacity Planning, Supply Chain and Collaborative.
-
Manufacturing initiatives.
Downtime Pareto
We understand the need to be more competitive and get the maximum throughput with your machine as assets in manufacturing.
To be able to “visualize” how quickly your machines are operating allows you to react quickly to situations. Measuring what actually happens on the shop floor allows you to fine tune your processes using LEAN manufacturing techniques. By applying the Theory of Constraints principle to monitoring and identifying a constraint, you can improve operator productivity and satisfaction by helping them perform faster, reduce their
data collection overhead, all by using automatic and accurate tracking systems.
Overall Equipment Effectiveness – OEE – is the key performance indicator that drives this machine monitoring process forward.